Lithium Battery Production Process
Step 1: Pole piece production
-
1. Mixing
In the preparation of lithium battery electrodes, you first need to prepare positive electrode materials, negative electrode materials and electrolytes, and then mix, coat and dry them to prepare electrodes. Among them, the mixing of ingredients is the basis for the subsequent lithium battery process, and high-quality mixing is the basis for the high-quality completion of the subsequent coating and rolling processes.
Positive electrode ingredients: Mix the positive electrode active material, conductive agent, binder and solvent to form a uniform and fluid slurry.
Negative electrode ingredients: Mix the negative electrode active material, conductive agent, binder and solvent to form a uniform and fluid slurry.
-
2.Coating
The coating is to evenly coat the stirred slurry on the metal foil and dry it to make positive and negative electrode sheets. As the core link in the front-end process of lithium battery electrode production, the execution quality of the coating process profoundly affects the consistency, safety, and life cycle of the finished battery.
-
3. Electrode Roll-in
Rolling is to compact the coated electrode according to a certain compaction density to smooth the electrode's surface. The material particles are in close contact to reduce the resistance of the electrode and increase the energy density per unit volume, thereby increasing the energy density of lithium batteries. The flatness of the electrode after rolling will directly affect the subsequent slitting process, and the uniformity of the electrode's active material will also indirectly affect the battery core performance.
-
4. Slitting
Slitting is to continuously cut the wider roll of the electrode into several narrow pieces of the required width. The electrode encounters shearing and fracture failure during slitting. The smoothness of the edge after slitting (no burrs, no buckling) is the key to investigating the performance of the slitting machine. Therefore, burrs should be avoided in the incision during the cutting process, and dust should be avoided on the surface of the electrode.
-
5. Electrode Making
The production process uses ultrasonic spot welding of small rolls of the electrode to the pole tabs, affixing insulating glue, and cutting the electrode into specified lengths for subsequent winding processes.
Step 2: Battery Cell Production
-
1. Winding
Winding is to separate the positive and negative electrode sheets with a separator and roll them into a roll core (the cell of a lithium-ion battery) of a specific size. It is mainly used for the production of square and round lithium batteries.
Winding machines can be subdivided into square winding machines and cylindrical winding machines, which are used for the production of square and cylindrical lithium batteries respectively. Compared with cylindrical winding, the square winding process has higher requirements for tension control, so the square winding machine technology is more difficult.
-
2.ALF Shaping
ALF shaping is punching aluminum plastic film into a shell of a specific size to facilitate the packaging of the battery cell.
-
3. Assembling
Put the rolled cell into the punched aluminum-plastic shell film, and seal the aluminum-plastic film into a bag with side openings.
-
4. Baking
During the production process of battery cells, a certain amount of moisture will be introduced. If the moisture is not controlled within the standard in time, it will seriously affect the performance and safety of the battery.
Generally, an automatic vacuum oven is used for baking. The cells to be baked are placed neatly, the desiccant is placed in the oven, the parameters are set, and the temperature is raised to 85°C (taking lithium iron phosphate cells as an example). Several vacuum drying cycles are required.
Baking process: heating, vacuuming, nitrogen replacement. These three steps act as a cycle. Bake for about 6 to 10 cycles. In this way, the moisture content of the electrode can be controlled to within 150ppm. After completion, cool the battery temperature to normal temperature and fill it with liquid.
-
5.Electrolyte Injection
Conduct a moisture test on the baked battery cell. Only after it meets the previous baking standards can you proceed to the next step: injecting electrolytes.
Liquid injection is to inject a certain amount of electrolyte into the battery cell to wet the electrode and separators. The liquid injection process includes entering the warehouse, filling the liquid, vacuuming, and sealing once.
Quickly put the baked cells into the vacuum glove box, weigh them, record the weight, and put them on the liquid injection sleeve. Add the designed weight of the electrolyte into the cup and put it into a vacuum box to evacuate to accelerate the penetration of the electrolyte into the electrode.
After several cycles, take out the battery cell and weigh it to calculate whether the liquid injection amount meets the design value. Less need for rehydration. If it exceeds the limit, the excess needs to be discarded. until the design requirements are met.
After the liquid injection is completed, it needs to be left at 45°C for 24 hours before it can be transferred to the formation process.
Step 3: Battery Cell Assembly
-
The production goal of the back-end process is to complete chemical packaging. Up to now, the functional structure of the cell of a lithium battery has been formed.
The main processes in the back-end process include formation, volume fractionation, detection, aging, etc. These processes require high accuracy, efficiency, and consistency.
1. Formation
The formation is the activation of the battery cell through the first charge. During this process, an effective passivation film (SEI film) is formed on the surface of the negative electrode to achieve the "initialization" of the lithium battery.
The SEI film formation process will produce a small amount of gas (CO2, CH4, C2H6, etc.), so the aluminum plastic film will reserve airbags to store gas. Excessive moisture inside the lithium battery cell will lead to an increase in chemical gas production and will form HF remaining inside the cell. Later, it will cause corrosion of the metal, causing the battery cell to swell.
-
2. Degassing
The second sealing step involves extracting air from the formed battery cell and sealing it at a high temperature, cutting off excess airbags, and finally folding up the edge sealing to make a square battery.
-
3. Capacity Testing
Capacity testing refers to "analyzing capacity", which is to charge and discharge the formed battery cell according to the design standards to measure the capacitance of the battery cell. Charge and discharge the battery cell throughout the formation and capacity testing process.
-
4. Visual Inspection
The appearance inspection will first remove the PET film on the surface, and then use visual inspection to screen out cells with defects such as internal foreign matter, scratches, pits, contamination, bloating, damage, skewed tabs, and poor folding. Finally put it into a white test blister box.
-
5.OCV1 Testing
The OCV1 test uses an automatic OCV testing machine to test the voltage and internal resistance of the battery cell and record the data and test time.
-
6. Aging
Aging is to place the cells that have been tested by OCV1 in an aging room with an ambient temperature of 45°C for high-temperature aging.
This process needs to last at least 5 days. The battery cell is then cooled to normal temperature and prepared for OCV2 testing. The function of aging is to accelerate adverse reactions inside the battery, usually at a rate of 7 to 10 times that of normal temperature.
-
7.OCV2 Testing
The OCV2 testing uses an automatic OCV testing machine to test the voltage and internal resistance of the battery cell and record the data and test time. The device will automatically calculate the self-discharge rate K value of the battery at the corresponding point.
Step 4: Battery Pack
-
Battery pack generally refers to combined batteries and mainly refers to the processing and assembly of lithium-ion battery packs. This process mainly involves processing battery cells, battery protection boards, etc. into the products that customers want through the battery Pack process.
1. Battery Cell Test
By assembling individual battery cells, the cells are composed into different series and parallel battery packs. Lithium battery packs require batteries to have a high degree of consistency (capacity, internal resistance, voltage, discharge curve, life, etc.).
After the lithium-ion battery pack is formed, the battery voltage and capacity are greatly improved and must be protected and monitored for charge equalization, temperature, voltage, and overcurrent. At the same time, it must also meet the designed voltage and capacity requirements. Therefore, it is necessary to test the battery pack.
-
2. Trim the Tabs
Trim overly long tabs to better weld the protective plate.
-
3. Welding PCB/PCM
Standalone lithium-ion batteries cannot be directly connected to electronic devices for use. A protection circuit must be added to prevent battery overcharge, over-discharge, short circuit, and other phenomena.
The protective plate is welded to the lithium battery cell to protect the lithium battery. The PCM or PCB (Protection Circuit Module or Circuit Board) is the "heart" of the lithium battery pack. The functions of the battery protection board include overcharge protection, over-discharge protection, over-current protection, and short-circuit protection. This can avoid explosion, fire, and damage of lithium battery pack, etc.
-
4. Rubber Coating
Lagging is wrapping the protective board for better insulation, fixation, and appearance.
-
5. Glue Wrapping
Wrap glue to better fix the protective plate and battery.
-
6. Test
After the lithium battery cells are assembled, they must be fully tested using a comprehensive tester. Test the battery performance with a tester to ensure that the battery performance meets the specified requirements.
Test items include shipping voltage, over-current value, short-circuit protection function thermistor resistance value, etc. And the test data needs to be saved for future reference.
-
7. Shipping
The batteries are packed in boxes, and only after passing the random inspection by the quality department and issuing a shipping inspection report can the shipment be arranged. Finally, it is delivered to the customer through logistics.
Battery Production Equipment
Battery Laboratory
Battery Making Machine
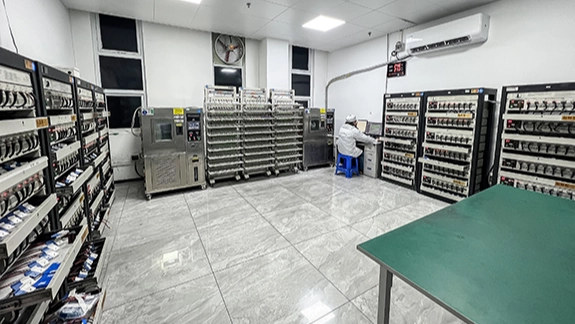
- 1. Capacity
- 2. Charge Recovery
- 3. Charge Retention
- 4. Charging Rate
- 5. Discharge Capacity
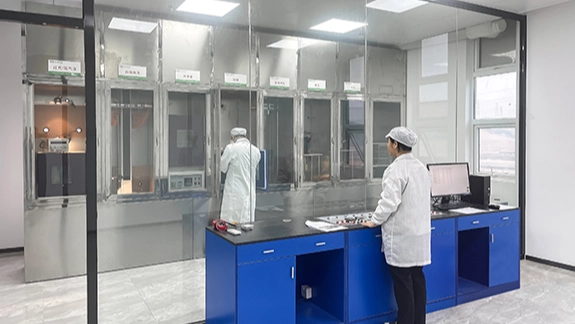
- 1. External short circuit test
- 2. Crush test
- 3. Impact test
- 4. Nail penetration test
- 5. Other safety test
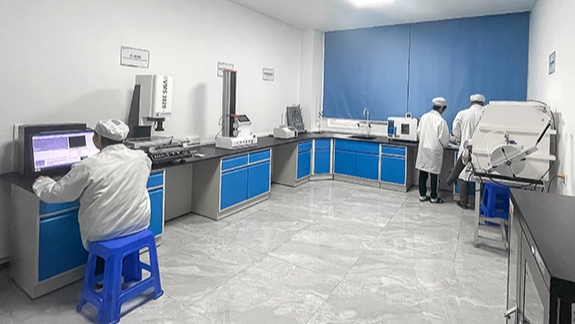
- 1. Density
- 2. Viscosity
- 3. Melting Point
- 4. Boiling Point
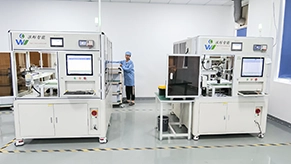
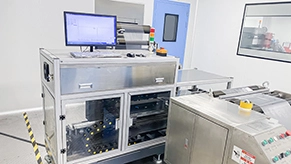
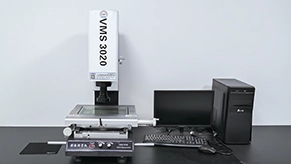
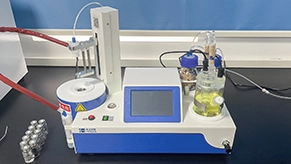
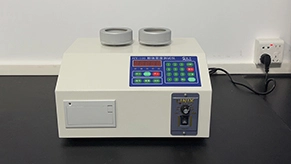
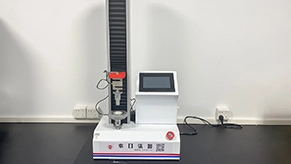